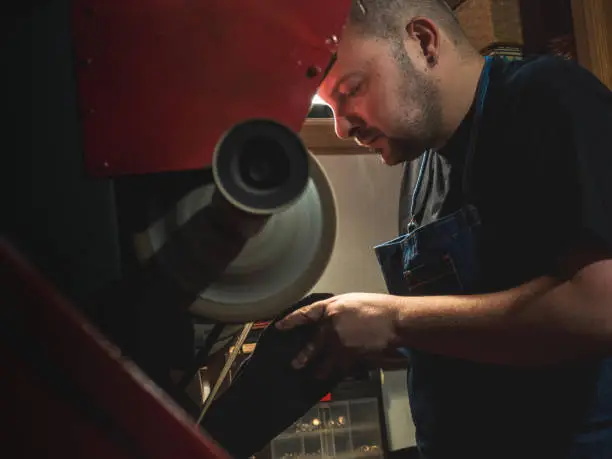
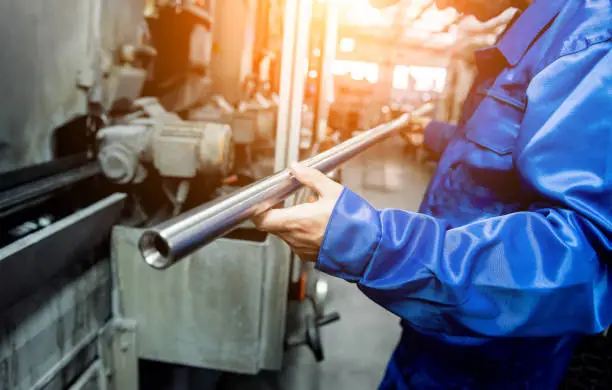
Top Trends in Metal Manufacturing 2025: Staying Ahead of the Curve
As we move through 2025, the metal manufacturing industry is at the forefront of technological evolution. The demands for efficiency, sustainability, and precision are driving transformative changes across the sector. For companies to remain competitive in this rapidly changing landscape, embracing new technologies is not just an option—it is essential.
At Tanfield Metal Spinners, we actively incorporate cutting-edge advancements to lead the way in innovation, ensuring our clients benefit from the latest metalworking technology. This blog explores the top trends in metal manufacturing for 2025, focusing on automation and sustainability—key factors shaping the industry’s future, particularly in the context of metal spinning.
Automation: Redefining Manufacturing Processes
Automation continues to revolutionise metal manufacturing by streamlining operations, enhancing precision, and addressing labour shortages. The integration of robotics and automated systems is now a staple in processes such as welding, cutting, material handling, and even metal spinning.
Collaborative Robotics
The rise of collaborative robots (cobots) has been a game-changer. Unlike traditional robots, cobots work alongside human operators, boosting productivity while maintaining safety standards. In metal spinning, cobots can handle repetitive tasks such as feeding blanks into spinning machines, enabling operators to focus on quality control and complex designs. At Tanfield Metal Spinners, we have two robots delivering providing assistance in our daily metal working activities.
Cobots improve production speed and reduce the risk of worker fatigue and injury, especially in demanding environments. Their adaptability to different tasks makes them ideal for scaling operations as demand increases.
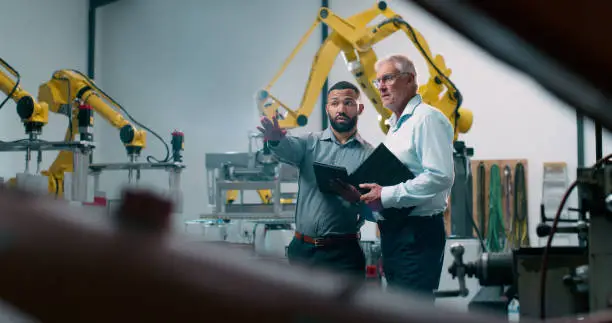
Advanced CNC Machines
Another critical development is advanced CNC (Computer Numerical Control) machines equipped with automated features. These machines offer exceptional accuracy in cutting and shaping operations, which directly benefits metal spinning by ensuring consistent and precise results for intricate geometries.
In metal spinning, CNC machines enable tighter tolerances and faster production of complex shapes. By integrating these machines with IoT technologies, manufacturers can achieve real-time monitoring and further optimise their processes.
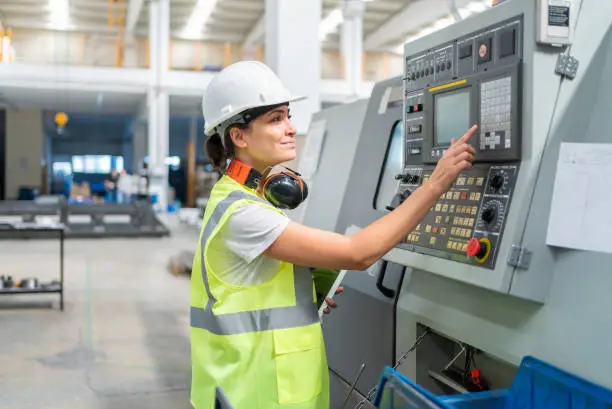
3D Printing: The Frontier of Innovation
Additive manufacturing, or 3D printing, has moved beyond prototyping to become a core component of metal manufacturing. 3D printing offers unparalleled design flexibility that complements metal spinning techniques by enabling the creation of complex geometries and customised components.
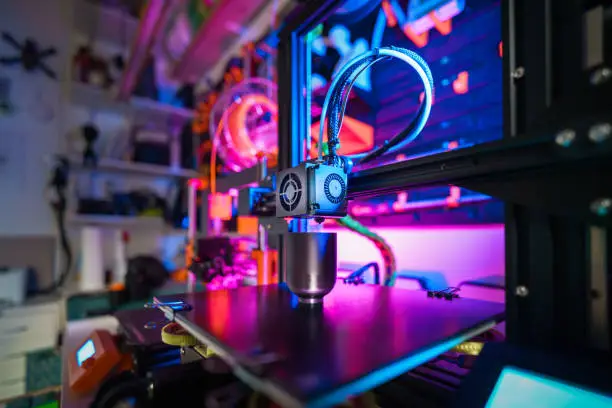
Sustainability Benefits
One of the standout features of 3D printing is its minimal waste. Technologies like metal powder bed fusion recycles unused material, reducing environmental impact. In metal spinning, this aligns perfectly with the industry’s goals of minimising material waste during forming processes.
3D printing also supports sustainability by enabling localised production, reducing the need for transportation and associated emissions. This capability makes it an excellent complement to sustainable practices in metal spinning.
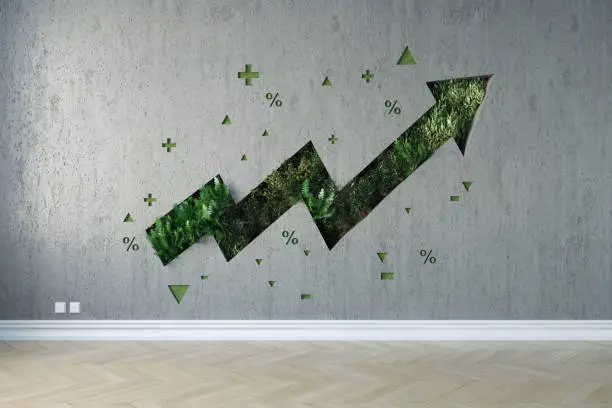
Applications
3D printing supports metal spinning by producing precise prototypes and tooling components. This aspect allows for faster development cycles and ensures tools meet exact specifications before production begins. The ability to create intricate designs and lightweight structures is particularly advantageous in industries such as aerospace and automotive, where performance and efficiency are paramount.
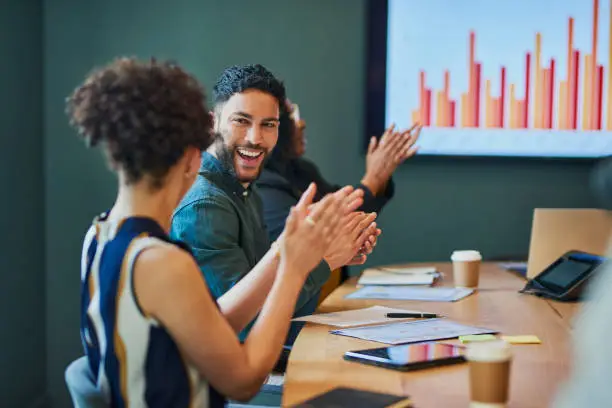
Sustainability: Driving Green Innovation
Sustainability is no longer optional but a core priority for the metal manufacturing industry. Companies adopting environmentally friendly practices reduce their carbon footprint and can meet stringent regulations, including those relevant to metal spinning.
Recycled Materials
The use of recycled metals is gaining momentum. Recycling conserves natural resources and reduces the energy required for production. In metal spinning, incorporating recycled materials can significantly lower the environmental impact of creating components such as lighting reflectors and kitchenware. Recycling also reduces the cost of raw materials, offering a financial incentive for manufacturers to embrace sustainable practices without compromising quality.
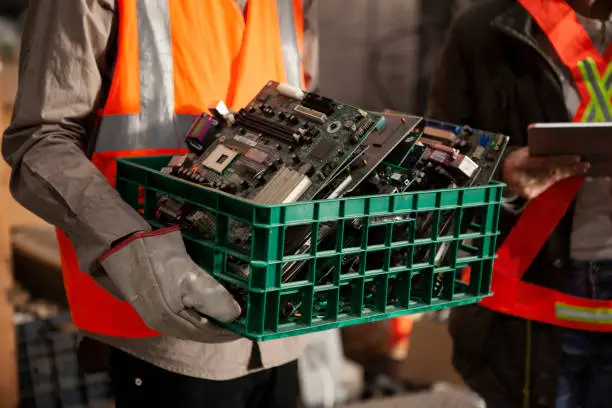
Energy Efficiency
Manufacturers are investing in energy-efficient technologies, such as renewable energy sources, to power their operations. This shift can leverage clean energy solutions to sustainably operate spinning lathes and related machinery. Equally, energy-efficient solutions include optimising machine usage to minimise idle time, further reducing energy consumption and operational costs.
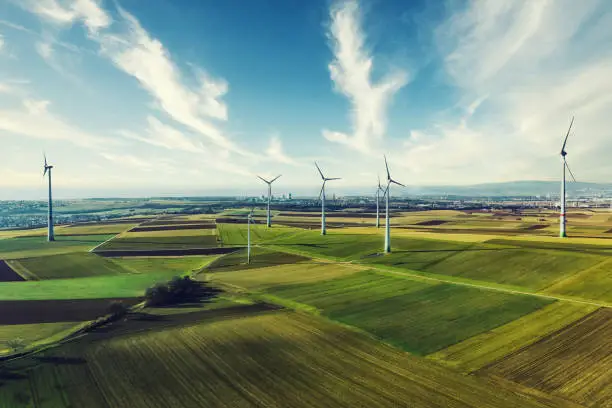
Advanced Coatings
Eco-friendly coatings, such as powder coatings with low volatile organic compounds (VOCs), can improve durability and reduce environmental impact. These coatings can be applied to spun components in metal spinning, enhancing their lifespan and performance in demanding environments.
Nano-coating technologies are also emerging, providing superior corrosion resistance and enabling spun products to perform in harsher conditions while maintaining environmental compliance.
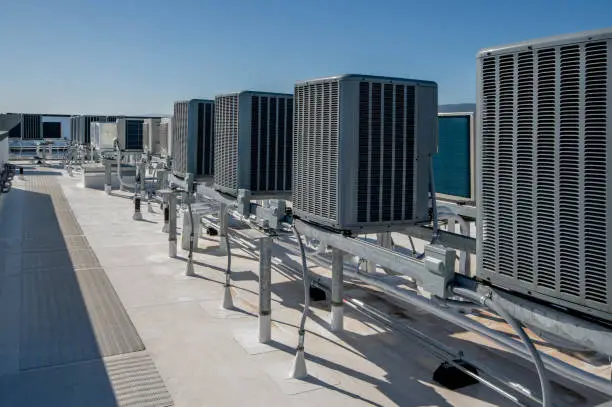
Smart Manufacturing: Harnessing Data for Precision
Digital transformation is reshaping metal manufacturing. Smart manufacturing leverages real-time data, advanced sensors, and artificial intelligence to optimise numerous production processes, including metal spinning.
IoT and Predictive Maintenance
The Internet of Things (IoT) enables real-time equipment monitoring, facilitating predictive maintenance and reducing downtime. In metal spinning, IoT sensors can monitor machine performance, detect irregularities, and prevent potential failures, ensuring seamless operations. Manufacturers can predict maintenance needs by analysing data and trends before issues arise, reducing downtime and improving overall equipment efficiency.
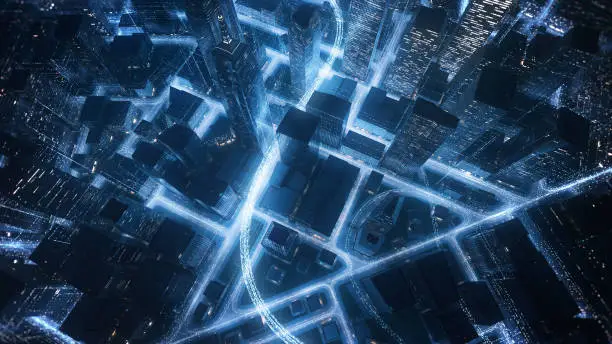
Digital Twins
Digital twins are virtual replicas of physical processes and are rapidly becoming indispensable tools. They allow manufacturers to simulate scenarios, test parameters, and refine processes before production begins. This technology ensures optimal machine settings and material usage for metal spinning, reducing waste and trial-and-error adjustments.
Digital twins also facilitate staff training, enabling operators to practice in a virtual environment before applying their skills to physical machines, enhancing productivity and reducing risk.
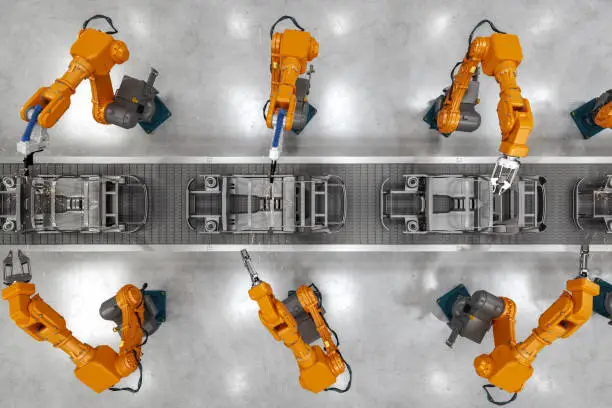
Robotics in Welding: Precision and Efficiency
Robotic welding systems are transforming the metal manufacturing landscape by delivering consistent, high-quality welds at an accelerated pace. These systems also complement metal spinning by enabling hybrid manufacturing setups.
Hybrid Welding Technologies
The combination of TIG and MIG welding methods within robotic systems allows manufacturers to handle a diverse range of materials and joint configurations. In metal spinning, robotic welding can be used to join spun components, creating larger assemblies with precision and durability. Robotic systems can also adapt to complex geometries, making them ideal for applications requiring high customisation.
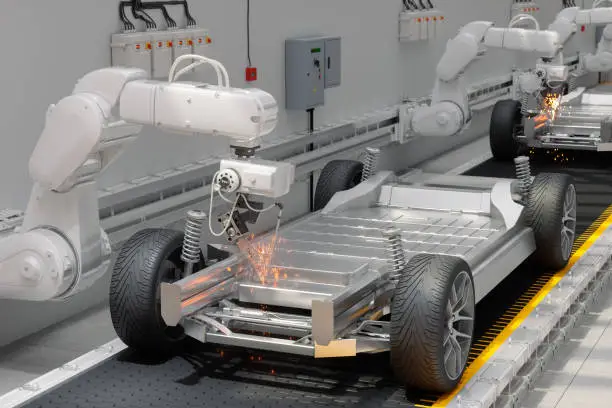
Advanced Materials: Expanding Possibilities
Advanced materials, such as high-strength steel, titanium alloys, and aluminium composites, are opening new possibilities for metal spinning.
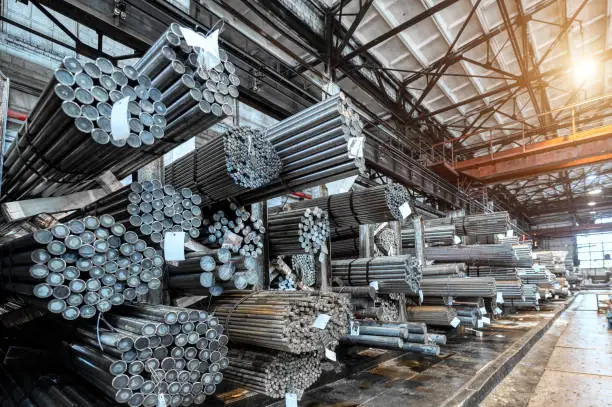
Applications Across Industries
Aerospace, automotive, and medical industries are among the primary beneficiaries of these materials. For example, high-strength aluminium alloys are ideal for spinning lightweight yet durable components for aerospace applications. With their superior strength-to-weight ratios, titanium alloys are increasingly used in spinning high-performance medical and industrial parts.
Advanced materials enable the creation of thinner yet stronger components, meeting demands for lightweight designs without sacrificing durability.
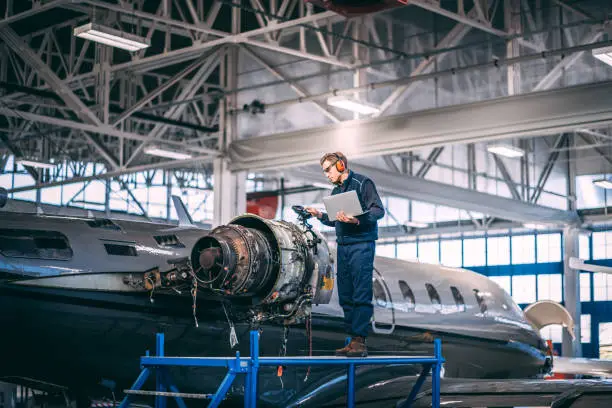